Решение проблемы эффективности процессов имеет два положительных эффекта.
Прежде всего, как мы видели, внедрение рулонной обработки в процесс дает экономию сырья, которая может даже превышать двадцать процентов для того же количества продукта, а это означает положительную прибыль и денежный поток, который доступен немедленно. в компанию.
Это может варьироваться в зависимости от сектора и использования: в любом случае это материал, который предпринимателю и компании больше не нужно покупать, а с отходами также не нужно обращаться или утилизировать.
Весь процесс намного выгоднее, и положительный результат можно сразу увидеть в отчете о прибылях и убытках.
Более того, закупая меньше сырья, компания автоматически делает процесс более устойчивым, поскольку это сырье больше не нужно производить на последующих этапах!
Энергоэффективность является еще одним важным элементом стоимости каждого производственного цикла.
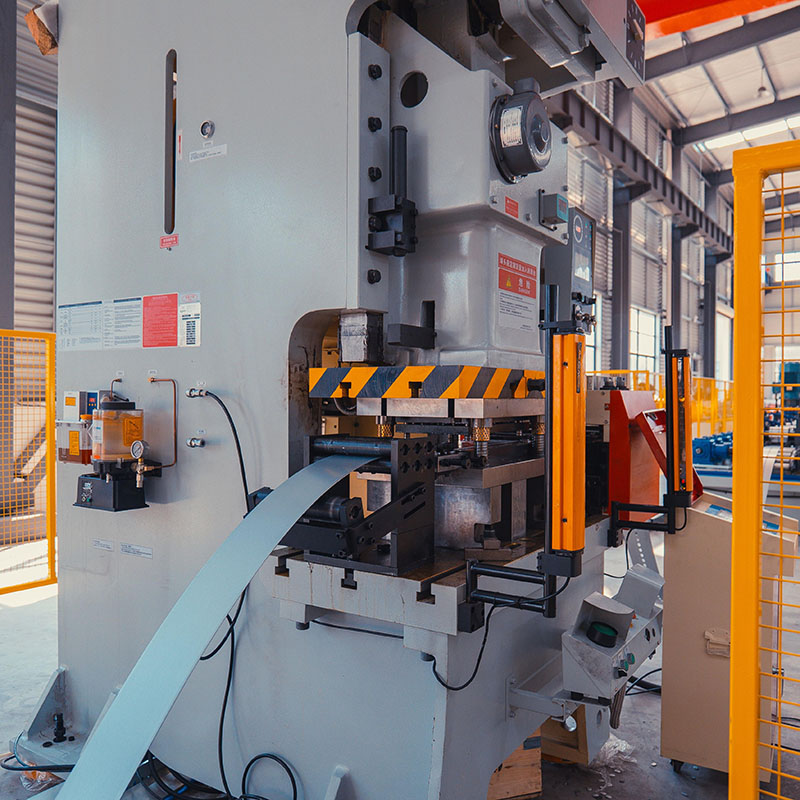
В современной производственной системе потребление профилегибочной машины относительно невелико.Благодаря системе Combi линии могут быть оснащены несколькими небольшими двигателями с приводом от инверторов (вместо одного большого специального двигателя).
Используемая энергия — это именно та энергия, которая требуется для процесса формовки, плюс любое трение в деталях трансмиссии.
В прошлом большой проблемой быстрых машин для резки была энергия, рассеиваемая через тормозные резисторы.Действительно, режущий блок непрерывно ускорялся и замедлялся с большими затратами энергии.
Сегодня, благодаря современным схемам, мы можем накапливать энергию во время торможения и использовать ее в процессе профилирования и в последующем цикле ускорения, восстанавливая большую ее часть и делая ее доступной для системы и других процессов.
Кроме того, почти все электрические движения управляются цифровыми инверторами: по сравнению с традиционным решением рекуперация энергии может достигать 47 процентов!
Еще одной проблемой энергетического баланса машины является наличие гидроприводов.
Гидравлика по-прежнему выполняет в машинах очень важную функцию: в настоящее время не существует сервоэлектрических приводов, способных генерировать такую большую силу в таком небольшом пространстве.
Что касается перфорационных машин с рулонной подачей, то в первые годы мы использовали только гидравлические цилиндры в качестве приводов для пуансонов.
Машины и потребности клиентов продолжали расти, как и размеры гидравлических силовых агрегатов, используемых на машинах.
Гидравлические силовые агрегаты создают давление масла и распределяют его по всей линии, что приводит к падению уровня давления.
Масло при этом нагревается, и много энергии тратится впустую.
В 2012 году мы представили на рынке первый сервоэлектрический перфоратор с рулонной подачей.
На этой машине мы заменили множество гидроприводов на одну электрическую головку, управляемую бесщеточным двигателем, развивавшим усилие до 30 тонн.
Это решение означало, что энергия, требуемая двигателем, всегда была только той, которая необходима для резки материала.
Эти сервоэлектрические машины также потребляют на 73% меньше, чем аналогичные гидравлические версии, а также обладают другими преимуществами.
Действительно, гидравлическое масло необходимо менять примерно каждые 2000 часов;в случае утечек или поломок трубок очистка и заправка занимают много времени, не говоря уже о затратах на техническое обслуживание и проверки, связанные с гидравлической системой.
Однако сервоэлектрическое решение требует лишь дозаправки небольшого резервуара со смазочным материалом, а машина также может быть полностью проверена, даже удаленно, оператором и специалистом по обслуживанию.
Кроме того, сервоэлектрические решения обеспечивают сокращение времени выполнения работ примерно на 22% по сравнению с гидравлическими технологиями. Гидравлические технологии пока нельзя полностью исключить из процессов, но наши исследования и разработки, безусловно, направлены на все более широкое использование сервоэлектрических решений из-за многочисленные преимущества, которые они предоставляют.
Время публикации: 23 марта 2022 г.